In traditional process improvement, teams spend most of their time on discovery and analysis, with value delivered primarily at the project's end. The hypothesis-driven approach, in contrast, focuses on the "why" before the "what." This method helps organisations understand opportunities holistically and concentrate efforts on the root causes of problems that will have the most significant impact.
We believe a hypothesis-driven approach should be driven by an ethos of informed thinking and focused testing, a holistic vision, and collaborative design. This approach to continuous improvement allows organisations to:
- Target process concerns and discovery work more acutely, focusing on value from day one.
- Maintain focus, prioritise, fail fast, and learn quickly, ensuring that we target the root cause of the problem and understand the “right” issues to address.
- Conduct hypothesis testing to generate insights for future sprints, identify recommendations that will offer tangible benefits, and build sustainable momentum within teams.
In this blog, we'll explore how you can put a hypothesis-driven approach into practice.
Value across three phases
A hypothesis-driven approach is most effective when divided into three sprint phases of about two weeks each. Defining clear outcomes at the outset of the sprint ensures value delivery, whether in the form of new, actionable insights or testable products. These phases include:
- Establish and prioritise hypotheses
- Experiment and learn
- Build
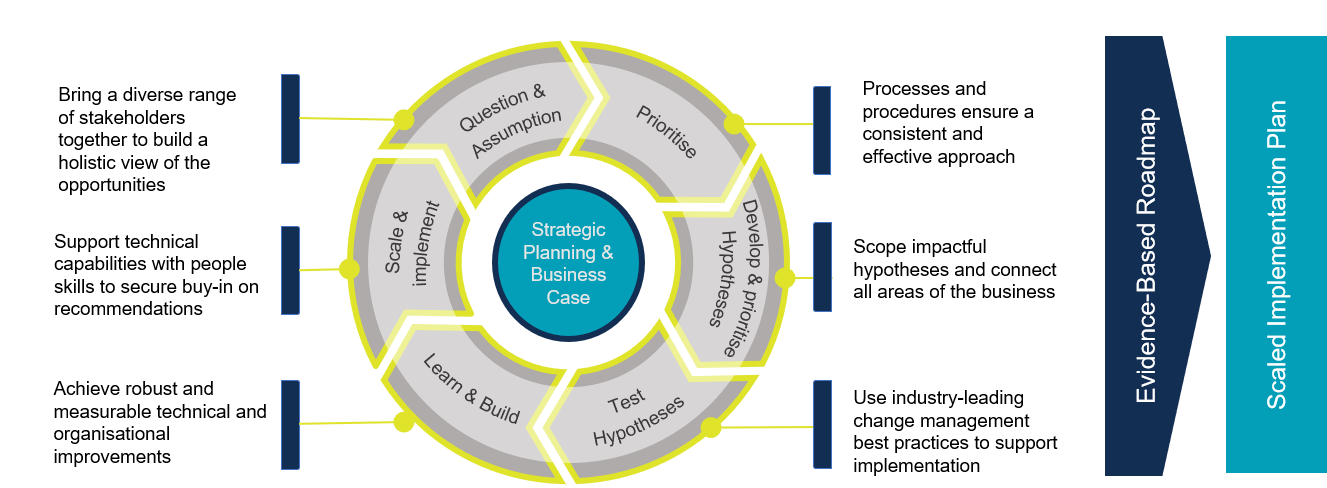
Phase one: Establish and prioritise hypotheses
In the first stage, form early assumptions, gather insights on key business challenges, and identify a set of root causes and hypotheses to test. The sprint team determines the level of analysis required to drive the desired outcome. It also decides how to prioritise activities for maximum results. Including internal stakeholders, and even considering outside SME perspectives, ensures collaborative learning. This approach enables the team to reprioritise hypotheses and test the right areas continuously. This phase usually takes one to three weeks, depending on the complexity of the problem.
Generating hypotheses with a top-down approach increases both the efficiency and effectiveness of decision-making. This technique also gives the sprint team a problem-solving roadmap that helps them ask the right questions, perform the correct analysis to find the answer, and deliver value quickly.
Working in this way makes it extremely easy for senior leaders to understand critical learnings, visualise results, and have an ongoing, robust dialogue to help the sprint team prioritise outputs that offer the greatest value.
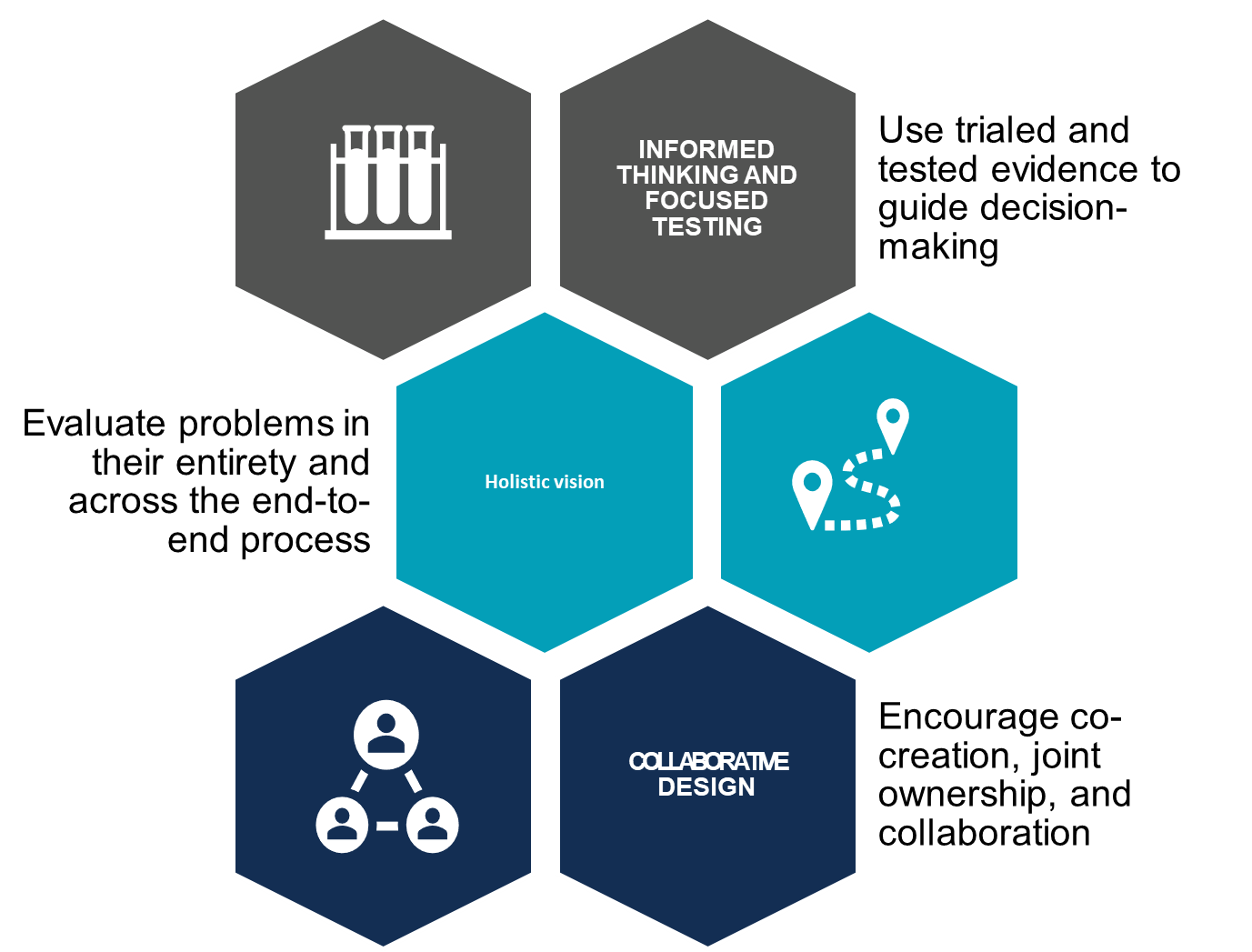
Phase two: Experiment and learn
The best way to test something is to do it. Testing hypotheses in a practical way minimises risk, combines quantitative and qualitative data to challenge the status quo, and offers evidence of solutions’ benefits when scaled. It also enables rapid data discovery, creates a forum for challenge workshops with the appropriate stakeholders, and identifies the level of risk associated with potential solutions. In this phase, it is also critical to test hypotheses through a cultural lens. In other words, observe behaviours and interactions across teams and leadership during the test phase. These observations can shed light on your organisation's appetite for change, along with the barriers standing in the way. From there, incorporate these insights into your roadmap. This approach bolsters employees' confidence in the solution. It also helps them understand the behaviours needed for the solution to land successfully and sustainably.
Throughout, expect each sprint to yield quantitative and qualitative insights, tested hypotheses, and proven recommendations that build throughout subsequent sprints. As you go, it’s critical to bring people along for the journey—helping to reinforce an organisation-wide appetite for change and a culture that encourages experimentation.
Phase three: Build
Once tested, incorporate solutions and recommendations into an evidence-based roadmap. The roadmap serves as an ongoing foundation to prioritise, implement, and create compelling business cases for internal change. Utilising a roadmap tool can further streamline this process, ensuring that all stakeholders have a clear view of the progress and future direction.
The optimal roadmap offers a mix of short-term and long-term initiatives to implement at your own pace. Alongside the roadmap, consider the additional tools and resources you will need to support the analysis. These assets can include the right people on your team, leadership sponsorship, business funding, technology, etc. Then, craft your recommendations.
Putting it into action
In practice, it looks something like this: We partnered with a government agency responsible for intellectual property and patents. It needed to reduce its patent backlog and limit future backlogs significantly. Using a hypothesis-driven approach, our team of Lean process improvement experts worked directly with the client’s leadership team and 500 patent examiners to:
- Test hypotheses with patent-examiner teams, quickly delivering a 27 percent reduction in the patent backlog.
- Create a tested, evidence-based roadmap of medium- and long-term recommendations with detailed scoping and scaling across the organisation.
- Increase patent-examiner capacity by 57 percent.
- Build sustainable momentum within several groups of patent examiners by deploying several recommendations.
As the organisation’s leaders found, the hypothesis-driven approach enables you to tap into informed thinking, focused testing, and a holistic viewpoint, co-creating solutions with people across the organisation. The result? Increased momentum and the internal capabilities needed to support ongoing change and improvement.
Traditional process improvement techniques devote a large proportion of time to discovery and analysis, delaying value until the project's completion. As we have explored in this blog, there is a better way. By focusing on the “why” before the “what” with a hypothesis-driven approach, you can evaluate opportunities from a broader vantage point—allowing you to orchestrate efforts for maximum value throughout the continuous improvement journey.